How Gas Detectors Work: A Beginner’s Guide
- Luke Dam
- May 30
- 4 min read
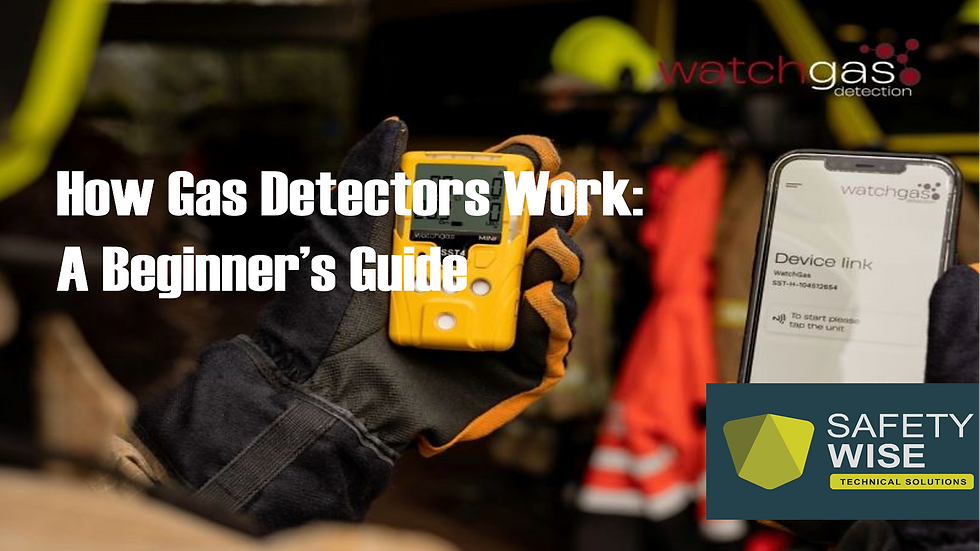
Gas detectors are a vital part of workplace safety, especially in industries where hazardous gases can pose significant risks to health, safety, and property. Whether you’re working in manufacturing, mining, oil and gas, utilities, or emergency services, understanding how gas detectors work can empower you to stay safe and act quickly in the face of danger.
This guide breaks down the basic science behind gas detection, the different types of gas detectors, how they function, and what users need to know to use them effectively.
Why Gas Detection Matters
Hazardous gases may be:
Toxic (e.g., carbon monoxide, hydrogen sulfide)
Combustible or explosive (e.g., methane, propane)
Asphyxiating (e.g., nitrogen, carbon dioxide in enclosed spaces)
These gases are often colorless, odorless, and invisible, making them impossible to detect without the help of a dedicated device. Gas detectors act as early warning systems, alerting users to the presence of dangerous concentrations before they reach harmful or explosive levels.
The Basic Principles of Gas Detection
At the heart of any gas detector is a sensor—a component that responds to the presence of a particular gas or group of gases. When gas molecules come into contact with the sensor, a physical or chemical change occurs. This change is converted into an electronic signal, which the device processes to display a reading or trigger an alarm.
Here’s a basic process:
Sampling the air – The detector draws in ambient air continuously or at intervals.
Gas interaction with sensor – If the target gas is present, it reacts with the sensor.
Signal processing – The change (in current, voltage, or resistance) is measured and converted into a readable value.
Alarm – If the level exceeds a pre-set threshold, the device alerts the user via audible, visual, or vibration alarms.
Common Types of Gas Sensors
Different types of sensors are used depending on the gas being detected. Each has its strengths and limitations.
1. Catalytic Bead (Pellistor) Sensors
Used for: Combustible gases (e.g., methane, propane)
How it works: When flammable gas comes into contact with a heated catalytic bead, it burns. The heat from combustion changes the resistance of the bead, producing a measurable signal.
Pros: Reliable for detecting a wide range of flammable gases.
Cons: Requires oxygen to function; can be damaged by contaminants like silicone or lead compounds.
2. Electrochemical Sensors
Used for: Toxic gases (e.g., carbon monoxide, hydrogen sulfide)
How it works: A chemical reaction occurs when the target gas comes into contact with the sensor, generating a small electrical current.
Pros: Highly sensitive, specific to certain gases, and low power consumption.
Cons: Limited lifespan; sensitive to humidity and temperature changes.
3. Infrared (IR) Sensors
Used for: Combustible gases (especially hydrocarbons), carbon dioxide
How it works: Gas absorbs infrared light at specific wavelengths. The sensor measures how much light is absorbed and calculates the gas concentration.
Pros: Long lifespan, works in oxygen-deficient environments.
Cons: Higher cost; not suitable for detecting hydrogen or acetylene.
4. Photoionization Detectors (PID)
Used for: Volatile organic compounds (VOCs), some toxic gases
How it works: Uses ultraviolet light to ionize gas molecules. The resulting current indicates concentration.
Pros: Fast response, sensitive to a broad range of organic compounds.
Cons: Requires calibration; can be affected by humidity.
5. Metal Oxide Semiconductor (MOS) Sensors
Used for: A variety of toxic and combustible gases
How it works: The sensor's resistance changes in the presence of gas due to interactions on its heated surface.
Pros: Durable and low-cost.
Cons: Less selective and more prone to false readings from interfering gases.
Types of Gas Detectors
Gas detectors can be categorised by their format and application.
1. Portable Gas Detectors
Carried by individuals.
Typically monitor for 1–4 gases.
Used for confined space entry, leak checks, or area monitoring.
Small, lightweight, battery-powered.
2. Fixed Gas Detection Systems
Permanently installed in hazardous areas.
Continuously monitor gas levels across large facilities.
Linked to alarms, ventilation, and shutdown systems.
Ideal for processing plants, refineries, and storage facilities.
Bump Tests and Calibration
Having a detector isn’t enough—it must work accurately.
Bump Test
A quick functional check to ensure the device responds to gas. A known concentration of test gas is applied, and the alarm should trigger. This test doesn’t measure accuracy, just that the sensor and alarms are functioning.
Frequency: Before each use or at least weekly.
Calibration
This adjusts the detector’s internal settings to match known gas concentrations. Over time, sensors “drift” and need recalibration to remain accurate.
Frequency: Usually every 30–180 days, depending on manufacturer guidance, usage, and conditions.
Key Features to Look For
If you’re choosing a gas detector, consider:
Sensor types and gas coverage
Alarm options (sound, vibration, lights)
Battery life
Display readability
Data logging capabilities
Durability and IP rating (dust/water resistance)
Common Use Cases
Confined Space Entry
Leak Detection
Environmental Monitoring
Fire and Explosion Prevention
Best Practices for Safe Use
Always bump test before use.
Calibrate on schedule.
Don’t ignore alarms—investigate immediately.
Keep sensors clean and dry.
Store in a cool, dry location.
Understand which gases your unit can and can’t detect.
Final Thoughts
Gas detectors are lifesaving tools that rely on solid science, regular maintenance, and proper use. They’re not “set and forget” devices—routine checks, calibrations, and training are essential to ensure they function correctly when it matters most.
Whether you're a safety professional, technician, or supervisor, learning how gas detectors work empowers you to make informed decisions and protect your team from invisible dangers.
Comentarios